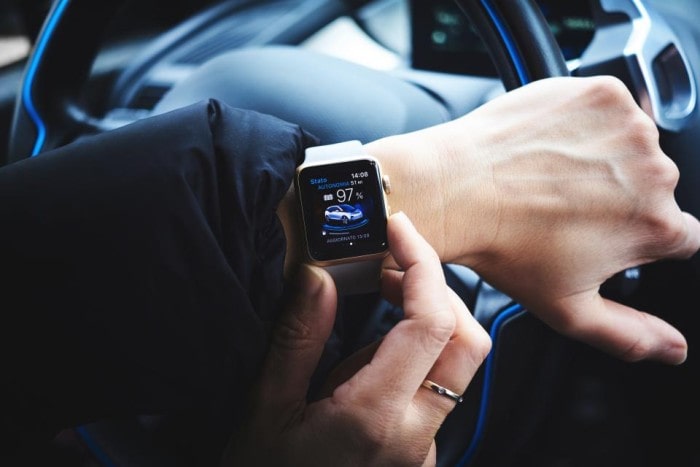
Conductive textiles and fibers are a new thing, but they could become the foundation of the future of clothing, upholstery, and more. As the name implies, these are textiles and materials that can conduct electrical current or signal. This makes them suitable for use in wearable electronics, in ways that smartwatches and things like Google Glass can only dream of.
However, there are a few challenges. The fact that these are new means that people haven’t quite caught on to their applications yet. There are also a few practical hurdles involved, not the least of which is figuring out how the textile industry can adapt to working with these materials.
The Makings of Conductive Fibers
First, let’s take a look at what these are made of. This will give the industry an idea of what it might expect. A conductive fiber is built out of conductive material wrapped around a non-conductive substrate. Usually, you’re looking at gold, carbon, nickel, silver, or titanium. The substrates used are cotton, nylon, or polyester. In effect, this makes them something between a fiber for fabric and a wire for electrical current.
Once properly made, a conductive fiber can actually be knitted, spun, woven, or stretched in much the same way as any other fiber. The key difference is that their conductive wrapping allows for them to transmit electrical signals. This means that with the right design pattern put into the equipment from a company like Xdknitmachinery, you can create clothing that has electronic functions while still being comfortable.
Flaws in the Plan
However, there are also flaws. In particular, conductive textiles don’t come with insulation, so they’re vulnerable to external noise and interference. The circuit inside your clothing itself could also cause such problems.
There is also erosion over time. The bond that connects the fibers with the conductive metal isn’t very strong, so that can wear down over time. The lack of insulation also means that conductor oxidation is going to be an issue.
Weaving or Knitting?
Now let’s take a look at how these fabrics are processed. In this case, your two options come down to knitting or weaving. Both have strengths and weaknesses, which can affect the exact details of what you can do or what is advisable.
Weaving
Weaving a conductive fabric provides a range of options. In terms of weight and electrical properties, you do have a wider range of choices. Weaving is also more stable in terms of electrical properties. The resistance is also low in most woven textile varieties, making them useful for data transfers.
However, woven fabrics have always had one weakness that making them conductive can’t fix. Woven fabrics are not as stretchable as their knitted counterparts. They’re also not prone to conforming to the body or draping over it, which can limit their applications from a fashion point of view.
Knitting
Knitted fabrics are better suited if your plan requires the use of traces and switches, and thus have a more complicated circuit board. Light to medium fabrics are easy enough to find, and if you need the material to have the ability to stretch, knitted is the way to go.
A knit fabric also has the ability to softly bend around a curve, something that weaving the textile won’t be able to do. Resistance can also be changed through stretching of the threads, which provides a few options.
On the other hand, resistance will change as the person wearing the clothing will move. That can cause inaccurate readings from sensors, as well as block how the current can get into things like LED lights and other components in the circuit. If your circuit is needed for fine-tuned values, then you don’t want to use them in knitted form.
Cutting the Fibers
Another issue you might encounter when dealing with conductive fibers is cutting. There are materials that are soft and feel like regular fabric, while there are others that are coated in bonding agents that make them stiff. This means that cutting the fabric can be a challenge. A “fabric-only” scissor won’t handle the job, but more heavy-duty ones could do the job.
Scissors
Scissors are the most accessible, and they’re also quick. They’re easy to use in a collaborative project, such as prototyping. However, the materials can chip at the edge and make them dull very quickly. Cutting by hand is also a slower process and one that is problematic for intricate work.
Lasers
Another viable method of cutting is through the use of a laser. This is going to be much more expensive, and one that is likely only going to be used in an industrial context. However, it does support far more intricate designs than other methods. It is also very fast, allowing for shorter production cycles before the fabric is processed into a finished product.
Conclusion
Working with conductive textiles can be an exciting process because it’s new and there are so many opportunities to innovate and be creative. However, it isn’t easy. While it is still a fabric, there are many changes made due to the conductive metal components. Still, this technology does make the possibility of smart clothing seem all the more real.